Effizienter produzieren – dank toii®
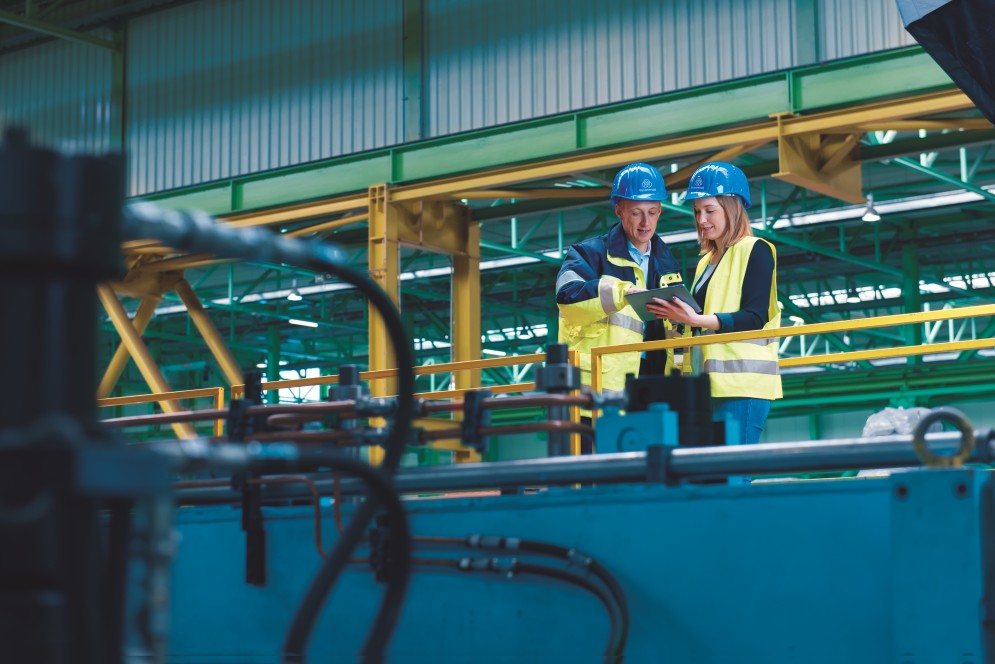
thyssenkrupp Materials IoT konnte mit Hilfe seiner Industrial Internet of Things (IIoT)-Plattform toii® Produktionsprozesse bei der thyssenkrupp Materials Processing Europe (MPE) flächendeckend automatisieren und optimieren.
Die Herausforderung für thyssenkrupp Materials IoT
MPE bietet am Standort Stuttgart die maßgeschneiderte Anarbeitung von Werkstoffen an. Drei Längsteilanlagen schneiden auf individuelle Anforderung der Kund:innen schmalere Bänder aus den Coils. Um das Unternehmen für die Herausforderungen der Zukunft zu rüsten, sollten die Prozesse nun weitgehend automatisiert sowie die vor- und nachgelagerten Prozesse digitalisiert werden.
In der Praxis bedeutete dies für die thyssenkrupp Materials IoT: Die einzelnen Geräte in der Produktionslinie sollten miteinander vernetzt und deren Produktionsdaten für weitere Anwendungen verfügbar gemacht werden. Handschriftliche Eingaben der Bediener:innen sollten in Zukunft durch digitale Daten ersetzt werden. Dies galt auch für die verwendeten Messverfahren: Sowohl die Breiten- als auch die Dickenmessung sollten digitalisiert und automatisiert werden. Zudem sollte ein Warenwirtschaftssystem (ERP) auf SAP-Basis in die digitale Umgebung eingebunden werden.
Das Produktivitätsziel für die Anlagen lautete: Die Effizienz sollte steigen, außerdem sollte eine Grundlage für die flächendeckende Optimierung ähnlicher Produktionsanlagen geschaffen werden. MPE erhoffte sich zudem eine Verbesserung des Informationsflusses zu den vor- und nachgelagerten Funktionen im Unternehmen sowie eine Nutzung der gewonnenen Daten in Big-Data-Analysen, um aus ihnen künftig weiteren Mehrwert zu gewinnen.
Das Lösungsdesign
Die Lösung wurde von thyssenkrupp Materials IoT (unseren IIoT-Spezialisten) gemeinsam mit MPE erarbeitet. Grundlage der Prozessoptimierung bildete die Implementierung der Industrial Internet of Things (IIoT)-Plattform toii®. Zunächst wurden mit Hilfe des Moduls toii®. Collect die Maschinen angebunden, deren Maschinendaten erfasst und für die Nutzung im System aufbereitet. Insgesamt wurden auf diese Weise 15 Einzelaggregate vernetzt.
Neben den Maschinen mussten auch analoge Messsysteme, wie beispielsweise Messschrauben, digital angebunden werden. Die Messgeräte wurden mit einem Funk-Modul ins Netzwerk eingebunden und über das Modul toii®. PDC in die toii®-Plattform integriert.
Die Digitalisierung manueller Produktionsdaten übernimmt das Softwaremodul toii®.PDC. Über das Modul werden auch Daten durch die Maschinenbediener:innen erhoben, die bisher nicht verfügbar waren. Hierfür wurden Terminals mit einer Web-Oberfläche eingerichtet. Produktionsmitarbeiter:innen können dort Störmeldungen oder andere Daten direkt in die Datenbank der toii®-Plattform eingeben.
Mussten vorgelagerte Daten bisher manuell über das Bedienterminal des Aggregats eingegebenen werden, erfolgt nun das Übertragen der notwendigen Daten in die Maschinensteuerung vollautomatisch, fehlerlos und effizient über das Modul toii®.Control. Dazu gehören etwa Messwerte. Die Messmittel zur Breiten- und Dickenmessung der geschnittenen Metallbänder wurden durch automatische Messsysteme ausgetauscht. Die Dickenmessung erfolgt durch einen radiometrischen Sensor, der zur optimalen Messung der Banddicke die Legierungsanteile des verwendeten Materials kennen muss.
Als Schnittstelle zu Drittsystemen, wie z. B. SAP oder einem anderen Warenwirtschaftssystem (ERP), wurde der toii®. Integrator implementiert. Er eröffnet ein Universum an Möglichkeiten für die weitere Datennutzung und deren Integration.
Diese Schnittstelle wird auch für den Soll-Ist-Abgleich der gemessenen Kenngrößen verwendet, um sie den Mitarbeiter:innen in Echtzeit an den toii®.PDC Terminals anzeigen zu können. Messwerte werden als Ampeln dargestellt, so dass die Maschinenbediener:innen mögliche Abweichungen sofort erkennen kann. Eine automatische Eskalation ist in diesem Fall ebenfalls möglich.
Der Kundennutzen
Die Digitalisierung der Anlagen durch toii® ermöglichte eine nahtlose Integration der verschiedenen vernetzten Komponenten untereinander und mit der Umgebung. Durch die Automatisierung konnten prozessbedingte Stillstandszeiten ohne weitere Maßnahmen um mehr als zehn Prozent gesenkt werden. Die Bedienoberflächen von toii® ermöglichen der Maschinenmannschaft eine effiziente und ergonomische Bedienung und haben zahlreiche handschriftliche Vorgänge auf Papier aus dem Prozess eliminiert.
toii® liefert zudem zeitnah Informationen, die im Rahmen des Shopfloor Managements in die kontinuierliche Verbesserung der Technik und Abläufe einfließen. Das Projekt ist die Blaupause für einen flächendeckenden Rollout zur weiteren Performancesteigerung in der Unternehmensgruppe.