The Digital Transformation of Manufacturing: Industry 4.0
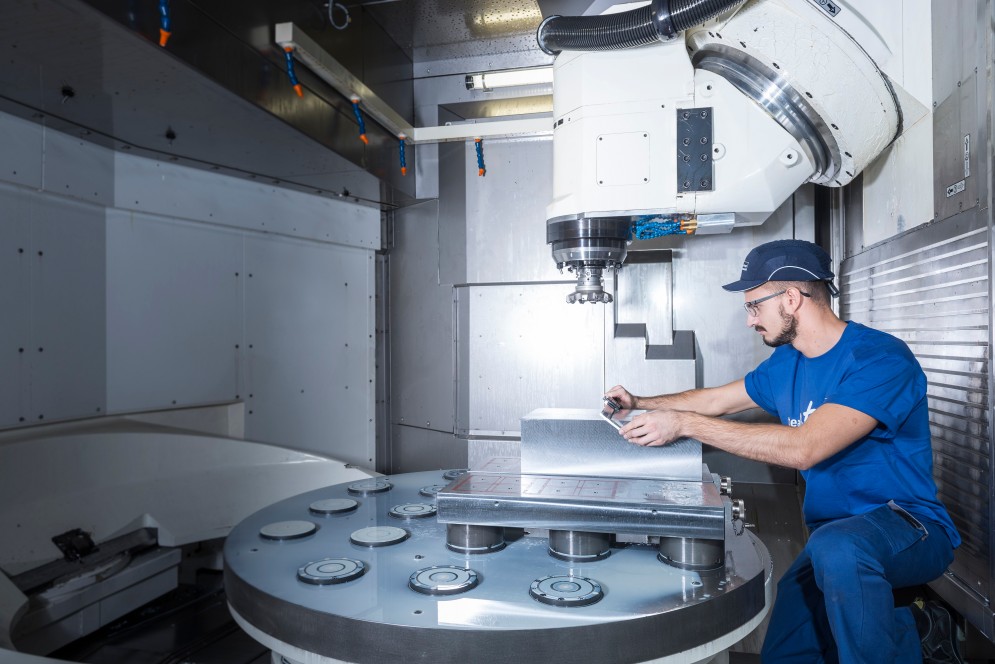
The IIoT platform toii® determines and analyzes basic data from 40 manufacturing components at thyssenkrupp Materials Schweiz AG – and thus serves as the basis for optimizing production.
The challenge for thyssenkrupp Materials IoT
thyssenkrupp Materials Schweiz AG supplies customers in the B2B sector with premium metals, including tool steel, powder metallurgy steel, stainless steel, structural steel, and many non-ferrous metals. Alongside pure distribution, the company also boasts an extensive range of machinery with a diverse number of processing options. Its key competences lie in chipping production – sawing, milling, grinding, deep hole drilling and 5-axis machining. It produces metallic semi-finished products with the highest quality requirements that are used in additive manufacturing, the aerospace industries, plastic injection molding applications, the watch industry, and medical technology.
The plant’s commitment to high quality means that it must continually monitor the machines and react quickly to any change in their statuses. A long-term analysis on the productivity of individual machines previously involved time-consuming logging and evaluations.
These processes were to be digitalized to prepare the company for its leap forward into the era of Industry 4.0. In doing so, the operating times and availabilities of all machines were to be automatically collected, made transparent, and manufacturing processes optimized.
The solution design
Specialists from thyssenkrupp Materials IoT worked on the solution together with colleagues from thyssenkrupp Materials Schweiz.They opted for toii® – the Industrial Internet of Things platform (IIoT) developed by thyssenkrupp Materials IoT to collect and merge the machine data.
The full range of machinery was connected to the IIoT platform using modules that had also been developed within the company. The modules determine the status of the respective machine, and transmit the report to toii® in the form of digital data. The IIoT platform processes this basic data, analyses it, and presents the results in a clear overview on a dashboard. Potential status changes are detected early on, downtimes are reduced, and machine productivity is increased.
Customer benefit
The full range of machinery at thyssenkrupp Materials Schweiz AG could be connected to the digital IIoT platform toii®. Merely automating processes made it possible to reduce downtimes by over 10 percent. toii®’s user interfaces enable the employees to operate the platform efficiently and ergonomically. Various paper-based, handwritten procedures have also been eliminated from the processes and replaced by digital datas. Media disruptions were prevented and thus also errors, such as those that could occur when rendering handwritten notes into digital documents.
Since commissioning, all information for production management that has been delivered by toii® is also fed back into the ongoing improvement of production processes. Technical sources of errors are detected and can be effectively eliminated.
The following optimization potentials were achieved with the aid of the logs, evaluations, and structured analysis of machine statuses:
By depicting the statuses on a dashboard, workers can react quickly in the event of failures or disruptions to restore productivity. For example, production failures due to missing material or electrical/mechanical machine errors can be identified straight away. The relevant personnel can be notified immediately.